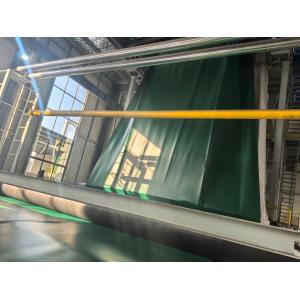
Add to Cart
Black and Green Dual-Color HDPE Geomembrane The Superior Solution for Impermeable Performance in Chemical Environments
Product Introduction
The black and green dual-color HDPE geomembrane is a new type of impervious geosynthetic material. It combines the advantages of high-density polyethylene (HDPE) and low-density polyethylene (LLDPE), manufactured through a double-layer co-extrusion blow molding process. This geomembrane features a black side and a green side, hence its name as the black and green dual-color HDPE geomembrane.
The black and green double-color HDPE geomembrane is made of HDPE or LLDPE polyethylene primary materials, with the addition of two different color masterbatches. The most common color scheme is black and green, hence the name black and green double-color HDPE geomembrane. Due to the higher requirements for raw materials in green, the production of this geomembrane must use new materials or first-grade white materials to ensure product quality.
The black and green dual-color HDPE geomembrane has high-strength tensile mechanical properties and excellent elasticity and deformation capabilities, making it very suitable for use on expanding or contracting base surfaces. Its water vapor permeability coefficient is extremely low (K≤1.0×10^-13 g·cm/cm²·s·pa), which can effectively overcome uneven settlement of the base surface and provide superior impermeable performance.
This geomembrane has excellent chemical stability and can resist corrosion from over 80 kinds of strong acid and alkali chemical media. This makes it perform excellently in environments such as sewage treatment, chemical reaction pools, and landfills.
The black and green dual-color HDPE geomembrane has excellent anti-aging, anti-ultraviolet, and anti-decomposition capabilities, allowing it to be used outdoors for more than five years. Additionally, the presence of the green side reduces the geomembrane's heat absorption capacity, thereby extending its service life.
The construction process is simple and fast. You only need to dig the pool and make corresponding leveling treatment, without pouring a concrete cushion layer. There is no curing period required for structural concrete, which greatly speeds up the construction speed.
The black and green dual-color HDPE geomembrane is widely used in various fields due to its excellent performance.
Landfill : Used for mid-surface covering, slope protection covering, and waste dump covering, etc.
Hydraulic Engineering: This includes the overall and local reinforcement of water-proofing for hydraulic structures such as reservoir areas, dam bodies, cofferdams, canals, artificial lakes, and water storage tanks.
Environmental Protection: Suitable for wastewater treatment, chemical reaction pools, and other environmental protection projects requiring impervious treatment.
Product Specification
* Thickness(mm): 0.30mm~3.00mm
* Width:1m~9m
* Roll length: 30m~100m (customized request accept)
PS: Customized request accept for all above.
Geomembrane Series
Smooth HDPE Geomembrane For Landfill (GH-2S & GB/T 17643-2011)
Specification | 0.75mm | 1.00mm | 1.25mm | 1.50mm | 2.00mm | 2.50mm | 3.00mm | Remark | |
Item | |||||||||
Thickness (mm) | 0.75mm | 1.00mm | 1.25mm | 1.50mm | 2.00mm | 2.50mm | 3.00mm | ||
Density (g/c㎡,≥) | 0.939 | ||||||||
Tensile Properties | |||||||||
Yield Strength (N/mm,LD/TD) | 11 | 15 | 18 | 22 | 29 | 37 | 44 | ||
Breaking Strength (N/mm,LD/TD) | 20 | 27 | 33 | 40 | 53 | 67 | 80 | ||
Yeild Elongation Rate (%) | 12 | ||||||||
Breaking Elongation Rate (%) | 700 | ||||||||
Rectangular Tear Strength (N) | 93 | 125 | 156 | 187 | 249 | 311 | 374 | ||
Puncture Strength (N) | 240 | 320 | 400 | 480 | 640 | 800 | 960 | ||
Environmental Stress Crack Resistance (h) (A single point of incision constant tensile method) |
300 | ||||||||
Carbon Black | |||||||||
Carbon Black Content(Rang) (%) | 2.0~3.0 | ||||||||
Carbon Black Dispersion | Nine of 10 observation area should be grade 1 or grade 2, not more than 1 of grade3 | ||||||||
Oxidative Induction Time (OIT) | |||||||||
Standard OIT (min) | 100 | ||||||||
High Pressure OIT (min) | 400 | ||||||||
85℃ Oven Ageing (Minimum Average) | |||||||||
90 days after baking, the standard OIT retention(%) | 55 | ||||||||
90 days after baking, the hight pressure OIT retention(%) | 80 | ||||||||
The Anti-UV Strength | |||||||||
Ultraviolet irradiation after 1600 hours, the standard OIT retention(%) | 50 | ||||||||
Ultraviolet irradiation after 1600 hours, the high pressure OIT retention(%) | 50 | ||||||||
-70℃ The Low Temperature Embrittlement Performance mpact | Pass | ||||||||
Water Vapor Penetration Coefficient g.cm (cm2.s.Pa) | ≤1.0X10-13 | ||||||||
Dimensional Stability | ±2 |
Product Specification and Technical Index (GH-1 & GB/T 17643-2011)
Specification Item |
0.30 | 0.50 | 0.75 | 1.00 | 1.25 | 1.50 | 2.00 | 2.50 | 3.00 | Remark | |
Thickness (mm) | 0.30 | 0.50 | 0.75 | 1.00 | 1.25 | 1.50 | 2.00 | 2.50 | 3.00 | ||
Density (g/c㎡,≥) | 0.94 | ||||||||||
Tensile Yield Strength (N/mm, ≥,LD/TD) | 4 | 7 | 10 | 13 | 16 | 20 | 26 | 33 | 40 | ||
Tensile Breaking Strength (N/mm, ≥,LD/TD) | 6 | 10 | 15 | 20 | 25 | 30 | 40 | 50 | 60 | ||
Yield Elongation Rate (%,≥,LD/TD) | - | - | - | 11 | |||||||
Breaking Elongation Rate (%,≥,LD/TD) | 600 | ||||||||||
Rectangular Tear Load (N,≥,LD/TD) | 34 | 56 | 84 | 115 | 140 | 170 | 225 | 280 | 340 | ||
Puncture Strength (N,≥) | 72 | 120 | 180 | 240 | 300 | 360 | 480 | 600 | 720 | ||
Carbon Black Content (%) | 2.0~3.0 | ||||||||||
Carbon Black Dispersion | Less than 1date of Grade 3 out of 10 data, grade 4,grade 5 is not allowed |